Summary Introduction: In the future, the wafer fabrication process will greatly reduce material costs. Ultra-thin saw blades made of diamond-coated nano-carbon materials cut silicon wafers with minimal kerf loss, greatly reducing material costs. Not in the sawing process
Introduction : In the future, the wafer fabrication process will greatly save material costs. Ultra-thin saw blades made of diamond-coated nano-carbon materials cut silicon wafers with minimal kerf loss, greatly reducing material costs. Sawdust is inevitably generated during the sawing process. If a large amount of sawdust is generated in the wafer fabrication in the photovoltaic or semiconductor field, the cost of material fabrication is very high; this kind of incision loss is relatively large compared to the product. The design and longevity are inevitable. Recently, scientists from the Fraunhofer Institute for Materials Research (IWM) in Freiburg, Germany, and the Commonwealth Scientific and Industrial Research Organization (CSIRO) have developed a new type of wire saw that greatly reduces the loss of the cut. This diamond-coated nano-carbon wire saw will replace the traditional impregnated diamond steel wire.
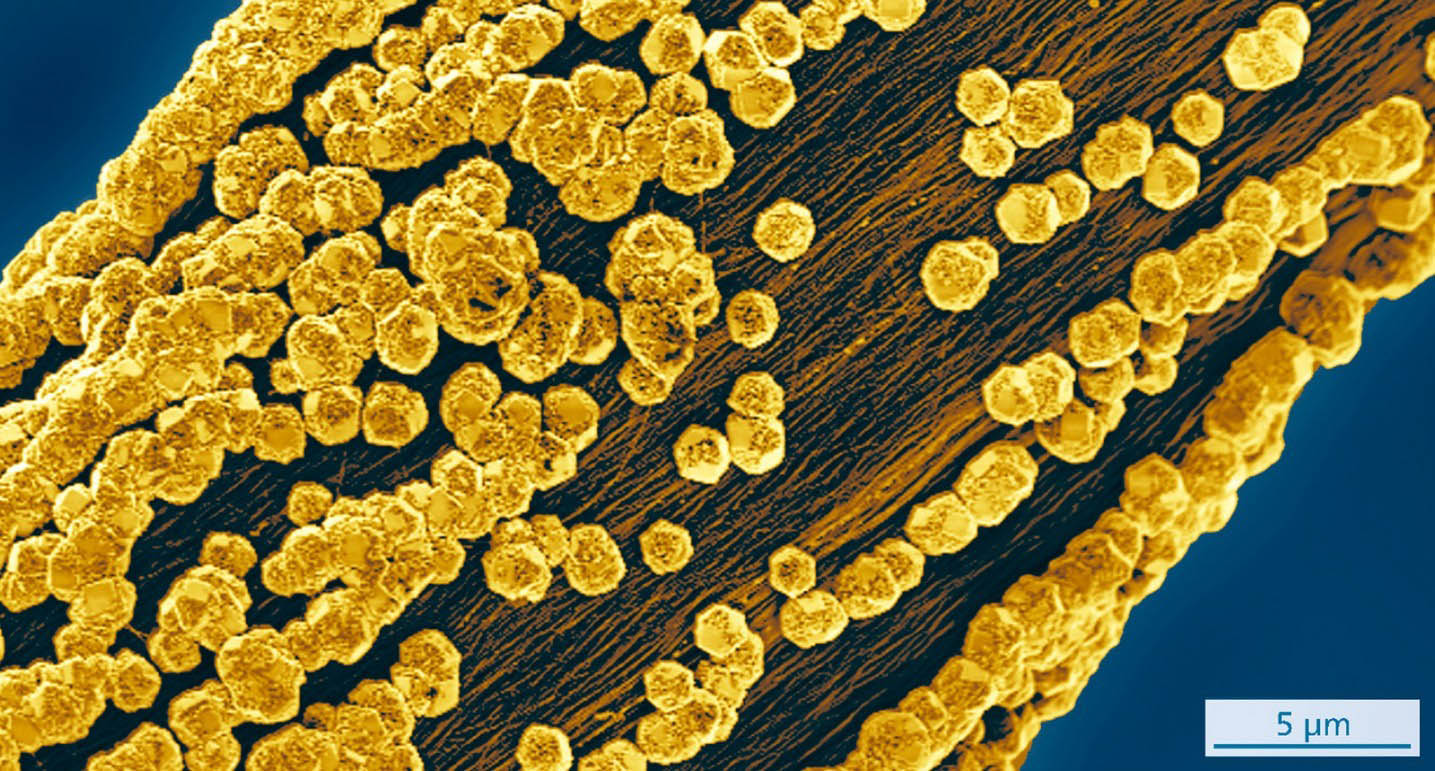
Diamond plated on the surface of carbon nanotubes
Manuel Mee, a scientist from IWM, explored a new way to protect fine carbon nanotubes in experiments. In the first stage of the experiment, the fused silica and the coating plasma in the reaction chamber reacted and deposited on the substrate to form a thin film, thereby functioning to isolate active hydrogen. Surprisingly, the diamond began to grow slowly on the silicon oxide film layer. "The formation of this film layer is quite special. It has not been done before. How to control the formation of this film and further optimization requires further research," Manuel Mee said. Through the transmission electron microscopy (TEM) of the Australian CSIRO laboratory, the staff found that the carbon nanotubes gradually "survived" under the protection of this layer of silicon oxide film.
How to diamond-plated nanowires made of carbon nanotubes is the focus of current research by IWM scientists. If successfully developed, this diamond-coated nanowire can be used to make ultra-thin saw blades and cut silicon wafers. . The Australian research team from CSIRO is currently the world's most authoritative nanocarbon pipeline production technology team. This technique requires special carbon nanotube "clusters" that, like ultra-thin blankets, are twisted into a very thin wire with a diameter between 10 and 20 microns. This diamond-plated wire can be used as an ideal material for a new generation of wire saws in the field of solar energy products. Manuel Mee explains: This new type of wire saw is much superior to traditional wire saws; due to its high tensile strength, the wire saw is thinner than a hacksaw, which reduces the loss of the cut more effectively. "(Compiled from "Saws made of carbon"; Translation: Wang Xian)
Chlorinated Hydrocarbon,Volatile Anesthetic,Cas No 79016,Cas 79-01-6
Yibin Tianyuan Group , http://www.ybtyco.com