With the rapid development of shipbuilding industry, the stability and safety requirements of marine centrifugal pumps are getting higher and higher. In order to improve the crew's working environment, ensure the physical and mental health of seafarers, reduce the vibration and noise caused by pump operation, The stability of pump equipment operation has become the direction of the future development of marine pumps. In this paper, the vibration and noise reduction of marine centrifugal pumps on a type of ocean-going vessel are studied and verified through experiments. Marine centrifugal pump should be how to reduce noise? 2 Reconstruction Object Brief introduction Marine centrifugal pump is mainly used for inhalation of seawater from the outboard, pressurized after the system piping sent to the water equipment or water, after the completion of the scheduled functions of discharge outboard. The original design parameters for the flow Q of 85dB, the pump is a single-shell pump, pump and motor rigid connection, the axial bearing thrust by the motor. Its structure is as shown. 3 Centrifugal Pump Vibration and Noise Analysis of the reasons Centrifugal pump is a kind of rotating fluid machinery, running due to mechanical and fluid dynamics causes vibration and noise. The vibration and noise are partly from the inside of the pump housing, which is directly related to the hydraulic pulsation of the fluid in the pump. The other part is directly related to the pump, which is related to the manufacture, installation and use of the pump itself. Concretely divided into the following aspects: Vibration and noise caused by poorly designed internal structure design unreasonable, resulting in uneven distribution of internal flow pump, pressure fluctuations in local areas, will lead to vibration and noise pump; if the design of the pump rigidity, Stiffness of the base plate is not considered, the calculation of the critical speed of the pump is error, etc., and the vibration and noise of the pump are also generated. Manufacture of low quality caused by vibration noise Marine centrifugal pump in the production if there is poor uniformity of the rotating parts, the pump impeller uneven mass distribution, uneven thickness of the blade, or impeller cover the local area thickness distribution is not so Appear, will make the rotor rotate the entire pump group to produce periodic excitation force, so that the pump body forced vibration, resulting in noise; impeller blade space shape is inconsistent, each blade produces different head lift rotation, so that Produce hydraulic imbalance and lead to increased vibration, but also make the pump vibration noise. When the pump is installed, the base is not level to find the reference plane, the pump shaft and the motor shaft do not meet the requirements of coaxiality, the pipeline configuration is unreasonable, the pipeline has stress and deformation, the foundation bolt is not firm enough, the vibration isolation device or component design, Improper layout or quality problems can also cause vibration and noise in the pump. When the centrifugal pump fixed frequency and some imbalance force excitation frequency coincide, it is possible to produce resonance, so that the pump vibration noise more intense. Improper use of vibration caused by the operation of the pump in the non-recommended operating conditions, and sometimes deviate from the design conditions is too large, resulting in greater radial force, the pump rotor force offset, or the pump body tension or compression According to past experience, the centrifugal pump may generate so-called "surge" when it deviates from the low-flow operation of about 60% -70% of the designed working condition. If the inspection of the pump operation state is lax, the external vibration Incoming, etc. can also cause pump vibration noise. 4 measures to improve From the above points to study the measures to reduce vibration and noise reduction, and marine centrifugal pump design, production process to be improved. 4.1 Design Improvement The pump and motor from the rigid connection to a flexible connection; change the pump shell structure, the pump body from a single shell designed as a double shell, and increase the shell strength, reducing radial force; improve pump assembly accuracy , Such as: to improve the accuracy of the coordination between the parts, the pump impeller, rotor components and rotor balance accuracy rating from G6.3 to G2.5 level; change the position of the pump plate stiffener and increase the number of pump inlet set to strengthen Tendons; motor bearings from castings to casting, in order to increase the vibration absorption capacity; Reasonable layout of the bearings to ensure that the elastic coupling after the pump itself to withstand axial force bearings. Improved pump structure as shown. In the process, some new equipment and techniques are adopted: the machining of the pump shaft is changed from the normal lathe to the CNC lathe; the lathe of the support is changed from the ordinary vertical lathe to the CNC vertical lathe; meanwhile, , An increase between the annealing annealing heat treatment, in order to better eliminate the cast steel in the process of internal stress generated to ensure the stability of the processing size. In order to ensure the impeller and shaft with the hole size increased from 7 to 6 precision, the process from the original turning to grinding; In addition, the impeller front and rear cover of the arc on the turning process from the original Ordinary sleeper processing into CNC sleeper processing. In order to ensure that the dynamic balancing accuracy of the impeller and rotor components is increased from the original G6. 3 to G2.5, the dynamic balance with a high precision dynamic balancing machine is used, and the minimum UMA is 0.1 gmm / kg The corresponding work instructions, the quality of this key process control. In order to better ensure that the unbalance of the rotor is controlled, special tooling is designed, that is, the impeller static balance and dynamic balance mandrel are used to control the unbalance of the impeller first, and then the dynamic balance test of the whole rotor is carried out. For the pump, pump cover and other pressure parts hydraulic test, preparation of hydraulic test operating instructions, to control the quality of its process. After the rough machining of the part, the hydraulic pressure test shall be carried out first. If there are any small defects such as sweating and leakage, repairs shall be made by means of welding repair and impregnation, and the hydrostatic test shall be carried out once the parts are finished. In order to improve the assembly accuracy of the pump and formulate a reasonable assembly process, in particular, to control the pulsation of the impeller port ring to the pump body, the impeller can not be checked after the pump body is installed, and the design pressure Cover instead of the pump port to locate. In addition, the assembly process, but also focus on the following processes check: motor shaft cylindrical flange on the motor side of the beat, the pump shaft cylindrical bearing stop beating the gap between the bearing gland and the bearing surface to Ensure that the pump and motor concentricity to meet the requirements. 4.3 Casting Process Improvements Two key components that affect the pump's hydraulic performance are improvements in the casting process for the pump body and the impeller. After changing the pump body from single shell to double shell body, the pump body divides the runner into two parts by the water diversion rib. Due to the distorted shape of the water diversion rib and the small volume of the whole pump body, it undoubtedly increases the difficulty of casting. Therefore, the design of the core tooling, respectively, the sand core channeling system, by the cords connected to form a whole sand core to ensure the integrity and compliance of the flow path. The mold design uses the metal mold combined with the plastic choke structure to ensure the even wall thickness of the castings. The castings are made of the whole body of chilled iron and resin sand, which is equivalent to the metal type casting to improve the compactness of the cast body structure and meet the pressure requirements. The wood mold into plastic mold, as far as possible to reduce the deformation of the mold casting process on the pump performance; in the mold making, in strict accordance with the size of the drawings and technical requirements of the production of leaves and runner sections of the cross-section of the sample and test Each section size. Due to many instability factors in the casting process, there is a certain deviation between the cast impeller and the design. The three-dimensional coordinate system is used to measure and compare the cast impeller with the designed impeller to guide the impeller casting and the mold modification. At the same time, the casting impeller adopts the principle of selecting the best and the best, selecting the impeller that meets the design requirements as much as possible and is in good agreement with the design for the assembly of the pump, so as to eliminate the influence on the pump performance caused by the manufacturing error of the impeller. 5 to improve the effect of the design of improved pump flow field simulation and floor modal analysis, and to improve the pump vibration noise test. Before the improvement of the total pressure distribution in the pump cloth, it can be seen that the pump body with double shell, greatly reducing the non-axisymmetric distribution of the flow field, thereby reducing the radial pressure and reduce the vibration of the pump. Table 1 shows the original welding base plate and improved casting base modal ten first order frequency, the pump system, the pump shaft rotation frequency of about 50Hz, the pump leaf frequency of about 300Hz, by comparison, foundry base Compared with the welding base has a higher natural frequency of each order, its greater impact on the first, second and third natural frequency, far more than the pump leaf frequency, not easy to resonance, so the casting base is more conducive to vibration and noise reduction. Table 1 before and after the improvement of the natural frequency of the base frequency contrast Hz natural frequency welding base casting base - second order third order fourth order fifth order sixth order seventh order eighth order ninth order ten steps Table 2 shows the improved pump operation under rated conditions vibration The noise index test results, the table shows: all the measured indicators are lower than the required value, the improvement effect is obvious. Table 2 Vibration noise after the improvement of the measured value and the required value of the comparison table item foot vibration body vibration air noise level index (dB) index (dB) required value of the measured value 6 Conclusion Centrifugal pump vibration noise from the starting point, a Type marine centrifugal pump was designed and manufactured to improve the pump after the flow field simulation and floor modal analysis and testing of vibration and noise during pump operation, the final test results show that the pump vibration and noise indicators to meet the requirements . It can be seen, the pump and motor from the rigid connection to a flexible connection to the pump body to make the design to make the pump flow more smoothly, improve pump assembly accuracy, change the position of the pump plate stiffener and increase the number of pump inlet settings Reinforcing ribs, the motor bearing from castings to castings, reasonable arrangement of the bearing to ensure that the elastic coupling after the pump bearing itself to withstand axial forces, these improvements can effectively reduce the vibration and noise of marine centrifugal pumps. Asia Fluid Network () Editor: Huang Nengwen, QQ:
As the different workpiece machined and working condition, we can offer and design the best router bit for your
situation. With their unique properties, our OPT woodworking cutters ensure max. machining productivity, and can be re-sharpened many times without affecting the original profile.
We have a world-class technical team, and can design cutting tools as individual situation.You can send us tool samples for checking, or wood samples for designing the right tools.
Woodworking Tools :
PCD Router Cutting Tools
PCD Wood Router Bit
Flexible in order quantity:
Samples can be provided before mass production, and MOQ can be discussed accordingly.
PRODUCT DETAIL:
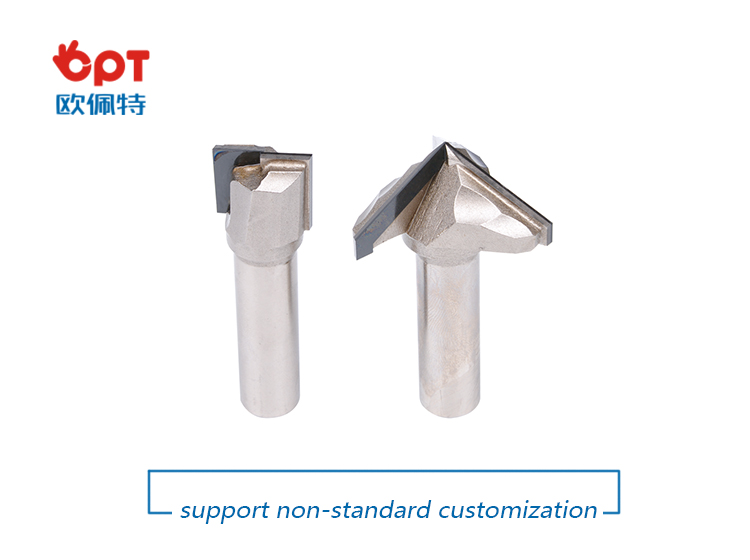
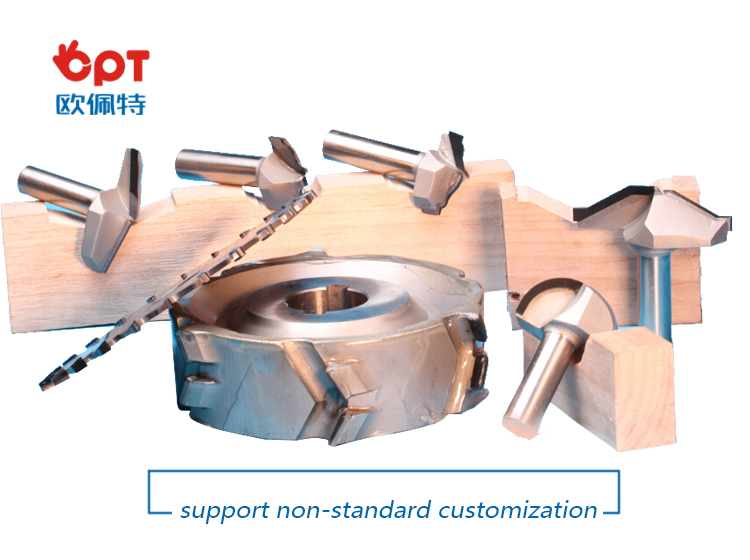
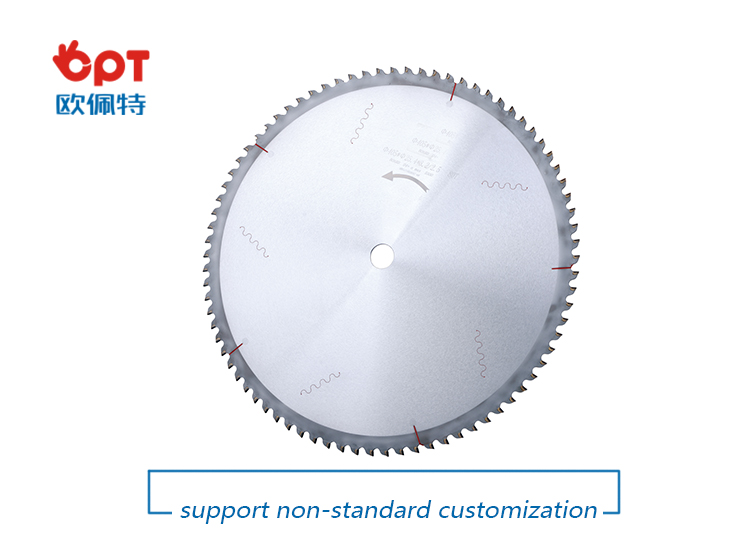
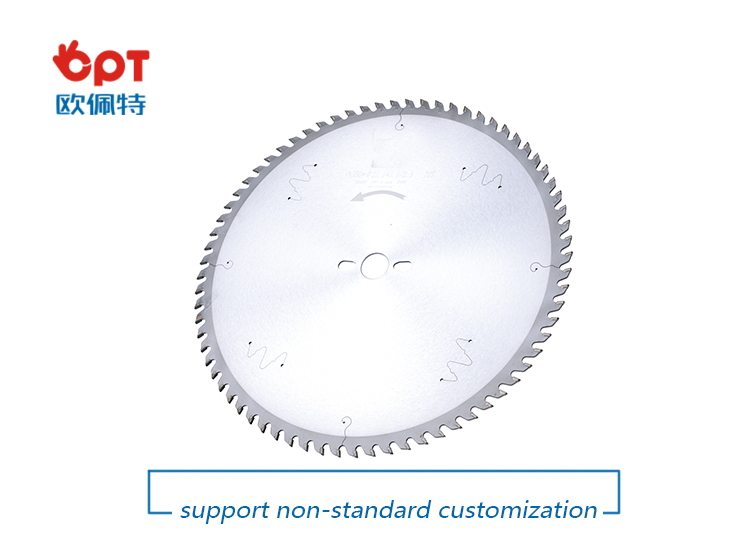
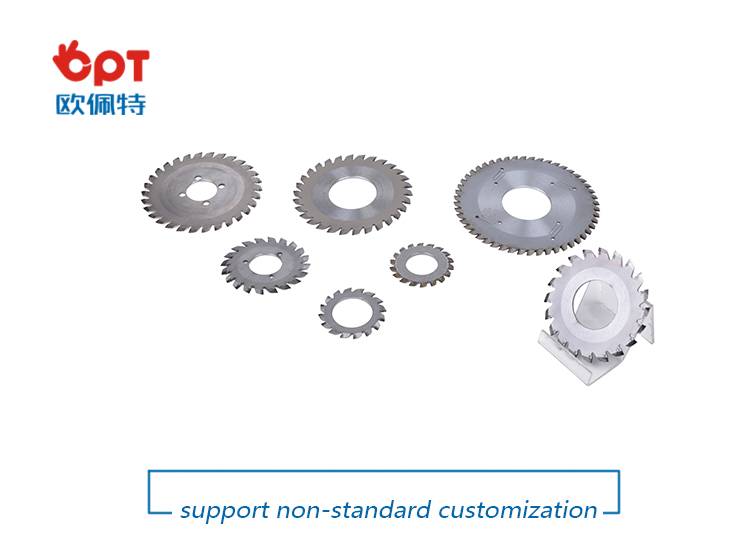
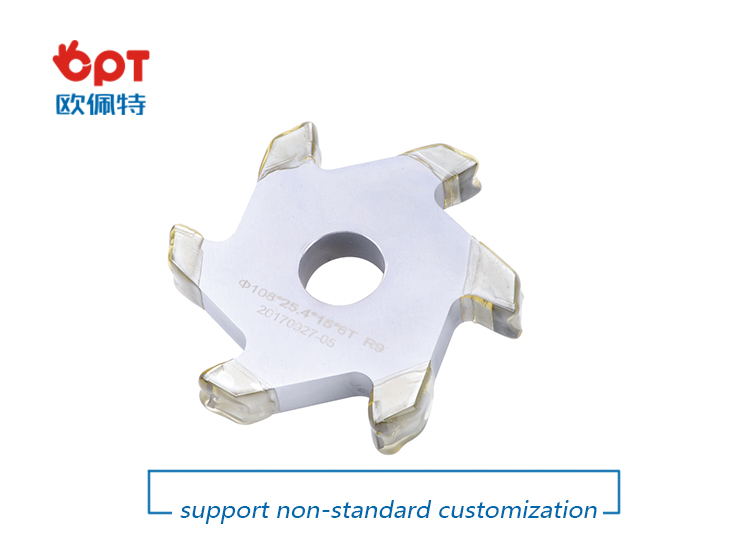
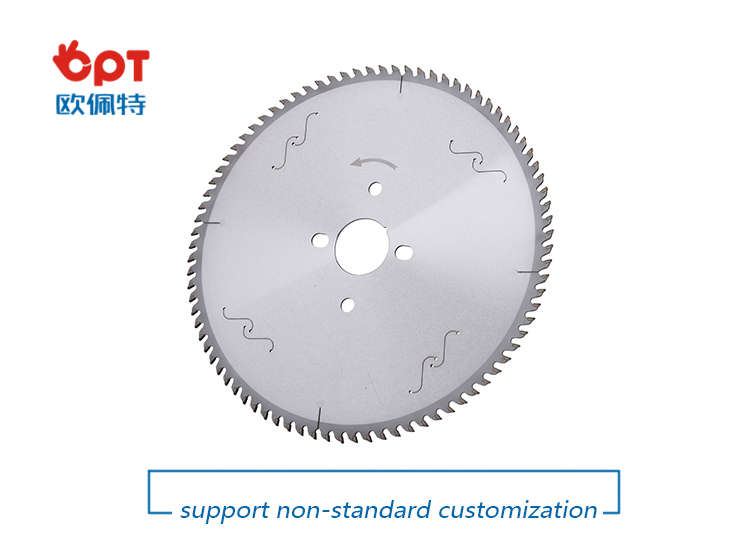
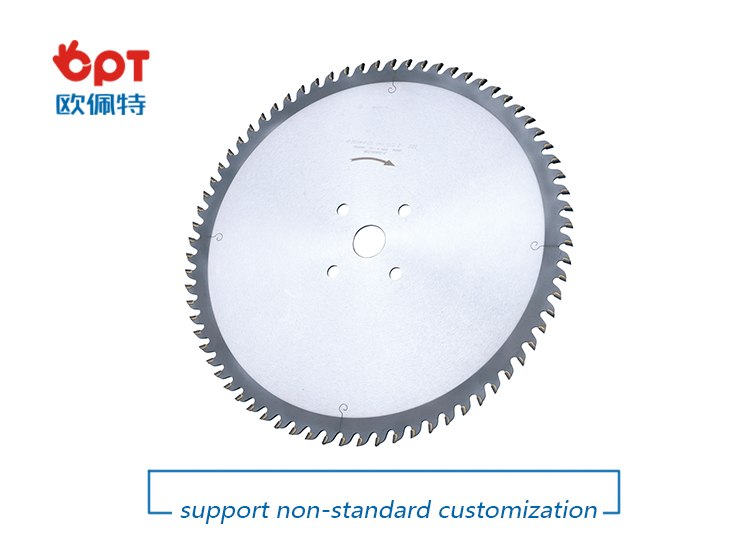
PRODUCTING PROGRESS:
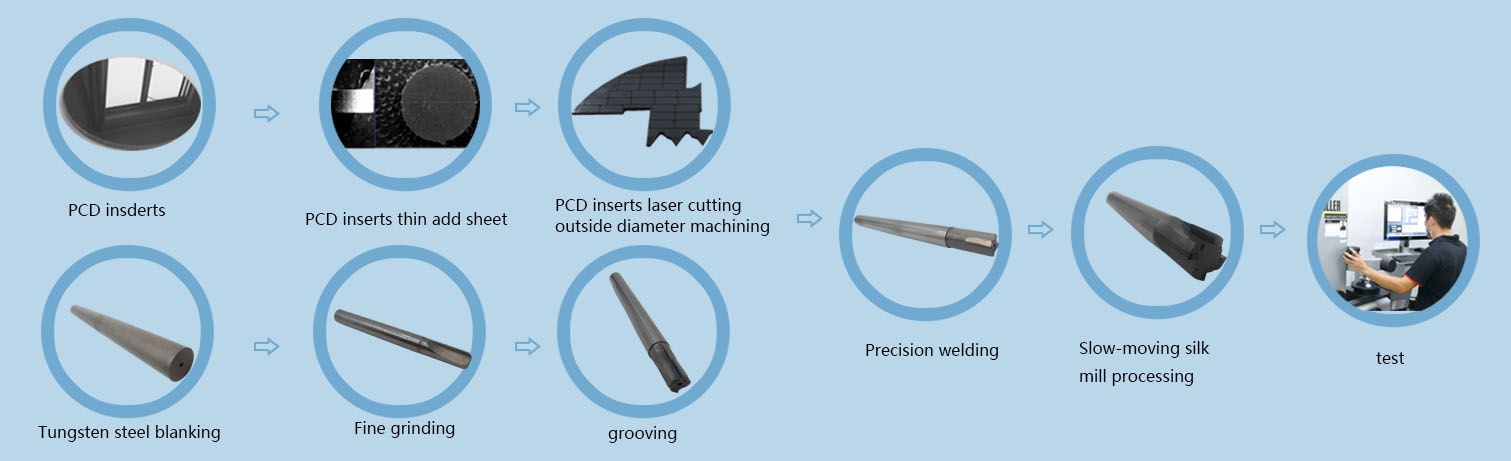
PAYMENT AND DELIVERY:
PRODUCT EQUIPMENT :
ABOUT US :
We are specialize in manufacturing PCD diamond tools and Carbide tools. Our major product inclulde PCD Inserts , PCD Reamers , PCD End Mills , PCD Taps, Cabide Inserts,Carbide Drills, Carbide Reams, Taps etc.,
We also offered customized cutting tools per drawings, and provide package according to customer requirements. We manufacture a series range of cutting tools for machining of Cast iron, Aluminium alloy and Non-Ferros metal, it is widely used in all major sectors like Automobiles, Engineering, Aerospace, Aviation and 3C industry. Premium quality of raw material is used in the production and strict examination during processing with advanced equipment, so our client are satisfied with our reliable quality and on-time delivery.
Our best selling of cutting tools include PCD Inserts, PCD End Mill , PCD Ball Nose Mill, PCD Reamer , Carbide Taps , Carbide End Mill , Special Form Cutter and many more. For these years we have been made a large forward in the technologies of manufacturing cutting tools. With high quality on performance and price, our product sells well both on domestic and overseas market. And we will always focus on the quality and best service, to make long business relationship.
quanlity control:
We have dedicated team of quality control and precise equipment to keep good and stable performance for our products and processing services.
PCD Wood Router Bit
PCD Router Bits,Diamond Drill Bit,Diamond Router Bits,PCD Wood Router Bit
OPT Cutting Tools Co., Ltd. , https://www.optdiamondtools.com